Casting silicone and polyurithane
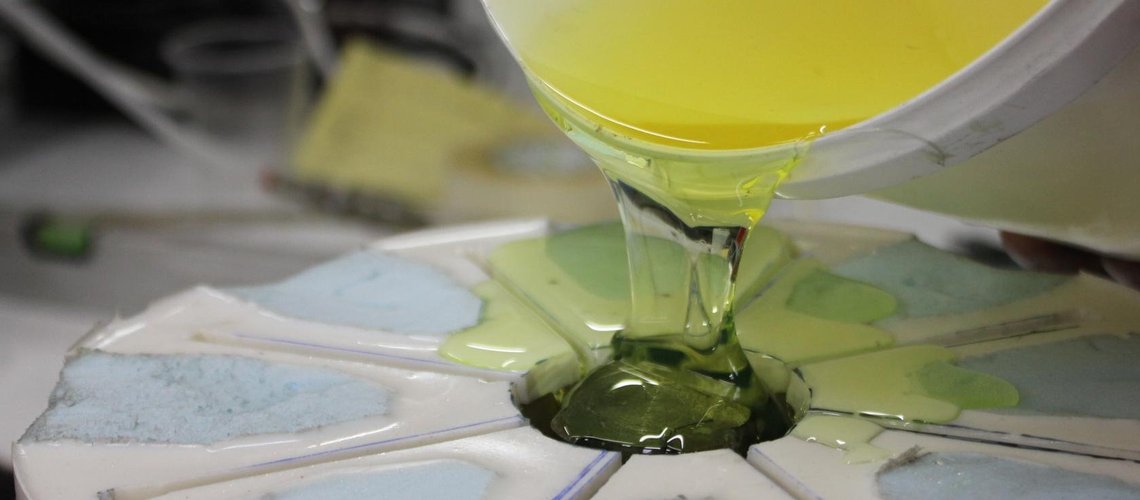
Liquid silicone
The material is a two-component system, which consists of a fluid part and a catalyst. When mixing the two components, the mixture begins to solidify, forming a durable product. Such silicone is optimal for making molds that are complex in configuration.
Silicones for molds come in 2 types: on a tin catalyst and on a platinum catalyst.
Both types have a wide operating temperature range, from -60 to +300°C, therefore, various types of resins, gypsum, wax, soap, plastic, and low-melting metals (such as tin) can be poured into these molds.
They also have a lot of positive properties, such as:
- ease of use, the ability to use at home,
- no residual deformation,
- nothing sticks to silicones (with the exception of silicone),
- silicone on a platinum catalyst can be used for the food industry.
Among the shortcomings can be identified:
- silicone does not hold alkaline compounds, so it is not advisable to pour concrete into them, the forms fail very quickly,
- silicones on a tin catalyst have low tensile strengths (if a crack has formed in the mold, then the mold breaks easily along this crack, therefore, when making the mold, it is advisable to additionally reinforce it).
Liquid polyurethane
It has a longer service life compared to silicone, it is softer than plastic, which helps to reduce rejects when removing products, but stronger than silicone, which allows casting stones from concrete without deforming the mold itself.
There are also 2 types: filled and unfilled polyurethanes.
Filled polyurethanes (the most economical option) are usually used for the subsequent pouring of gypsum, unfilled - for concrete.
Of the positive properties can be noted:
- very high tensile strength,
- high abrasion resistance,
- wide range of hardness from 30 to 95 shore A.
Of the shortcomings:
- maximum temperature up to 100 °C
- in the manufacture of the mold, a release agent is required.